In the realm of industrial machinery, the efficiency and precision of cutting tools are paramount. Beveled edges play a crucial role in determining the performance and longevity of machine knives used in various industrial applications such as printing, processing, converting, and packaging.
Let’s delve into the intricacies of different beveled edges and their optimal use cases in industrial applications.
Different Beveled-edge Designs
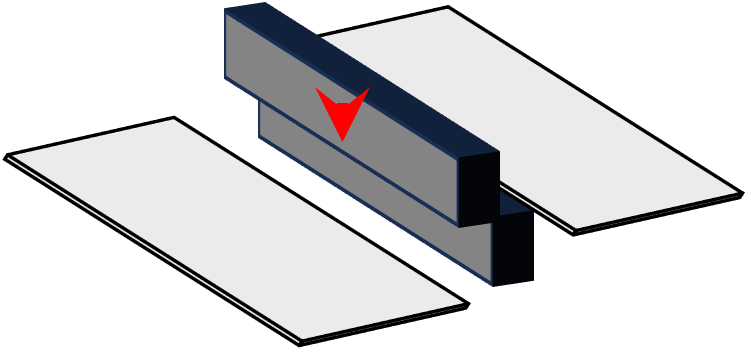
Square Edges
A square edge on an industrial machine knife refers to a cutting edge that is straight and perpendicular to the blade’s surface, without any bevel or angle. Essentially, it is flat with sharp corners where the blade meets the material being cut. This type of edge is commonly found on metal slitter blades and run in a set, with one knife on top of the material and one offset just below.
Benefits of Square Edges:
- Maximum Strength and Durability: Square edges offer exceptional strength and durability, making them well-suited for heavy-duty cutting tasks. Their robust construction enables them to withstand high levels of stress and pressure without deforming or dulling quickly.
- Suitable for Sheer Force Applications: In industries such as processing, where sheer force is more critical than precision cutting, square edges excel. They provide reliable cutting power, especially when slicing through thick materials like steel, cardboard, plastic sheets, or rubber.
- Minimal Friction and Heat Generation: Since square edges lack bevels or angles, they minimize friction and heat generation during cutting. This can be advantageous in applications where excessive heat buildup could compromise the material being processed or the cutting tool itself.
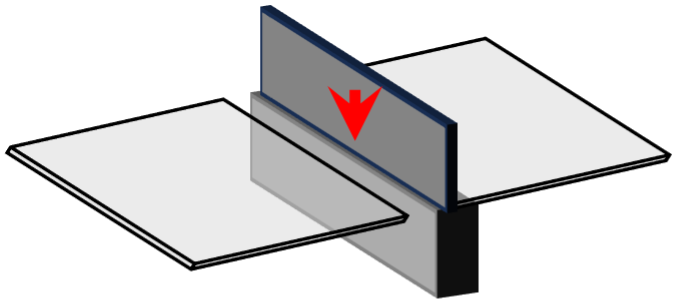
Single Bevel
A single-beveled edge on an industrial machine knife is characterized by having a bevel on only one side of the blade, leaving the other side flat. This creates a cutting edge that slopes down from one side of the blade to form a sharp angle, while the opposite side remains straight.
Benefits of Single-beveled Edges
- Enhanced Cutting Precision: Single-beveled edges offer superior cutting precision compared to square edges. The angled blade allows for a more controlled and accurate cutting motion, resulting in cleaner and more consistent cuts, especially on thin or delicate materials.
- Reduced Friction and Drag: The angled design of single-beveled edges reduces friction and drag during cutting, leading to smoother and more efficient cutting operations. This can be particularly advantageous in applications where smooth, uninterrupted cuts are essential, such as in printing or converting processes.
- Sharper Cutting Performance: The edge of single-beveled knives tends to be sharper than square edges, allowing for easier penetration into the material being cut. This sharpness translates to improved cutting efficiency and reduced required effort by the operator.
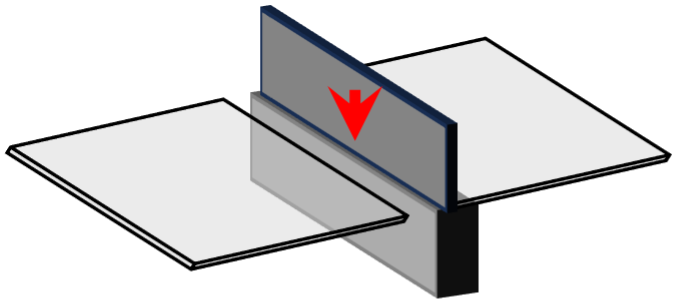
Double Bevel
A double-beveled edge on an industrial machine knife is characterized by having bevels on both sides of the blade, forming a V-shaped edge. This configuration creates two angled surfaces meeting at the cutting edge, providing a balance between cutting performance and ease of maintenance.
Benefits of Double-beveled Edges:
- Versatility: Double-beveled edges offer versatility in cutting applications due to their balanced design. They can handle a wide range of medium- to light-weight materials and cutting tasks with relative ease, making them suitable for various industries.
- Ease of Maintenance: Compared to single-beveled knives, double-beveled knives are generally easier to maintain. The symmetrical design allows for simpler sharpening and honing procedures, reducing downtime and maintenance costs for industrial operations.
- Balanced Cutting Performance: The dual bevels of double-beveled edges provide balanced cutting performance, combining the sharpness and precision of single bevel edges with the strength and stability of square edges. This makes them well-suited for faster and precision cutting tasks.
Different Bevel Angles and Widths
In addition to beveled-edge designs, various angles and widths are critical to achieving different cutting characteristics and optimizing performance for specific applications.
Acute Angles on Beveled Edges
An acute angle on beveled edges refers to an angle that is less than 30 degrees relative to the surface of the blade. This means that the cutting edge is very sharp and narrow, resembling a pointed wedge.
Benefits of Acute Angles:
- Exceptional Sharpness: Acute angles offer unparalleled sharpness, making them ideal for applications requiring fine cuts or working with delicate materials. The acute angle allows for precise penetration into the material, resulting in clean and precise cuts.
- High Cutting Precision: The sharpness of acute angles enables high cutting precision, allowing operators to achieve intricate detailing and precise dimensions in their cuts. This is particularly advantageous in industries, such as printing and converting, where precision is critical when cutting thinner materials.
- Reduced Cutting Force: Due to their sharpness, acute angles require less cutting force to penetrate the material. This can result in reduced wear and tear on the blade and machinery, as well as increased efficiency in cutting operations.
Moderate Angles on Beveled Edges
A moderate angle on a beveled edge typically falls within the range of 30 to 45 degrees relative to the surface of the blade. This angle provides a balance between sharpness and durability, making it a versatile choice for various cutting tasks in industrial applications.
Benefits of Moderate Angles:
- Versatility: Moderate angles offer versatility in cutting applications, making them suitable for a wide range of materials and cutting tasks. They strike a balance between sharpness and durability, allowing for effective cutting performance across different industries and applications.
- Balanced Cutting Performance: The moderate angle on a beveled edge provides a balanced combination of sharpness and edge stability. This results in reliable cutting performance with good edge retention, making moderate angles suitable for precision cutting and heavier-duty tasks.
- Ease of Maintenance: Compared to acute angles, moderate angles may require less frequent sharpening while still maintaining a sharp cutting edge. This reduces downtime and maintenance costs in industrial operations, improving overall efficiency and productivity.
- Suitability for Various Materials: Moderate angles can effectively cut a wide range of materials, including paper, cardboard, plastics, fabrics, and metals. This versatility makes them a popular choice in industries, including printing, processing, converting, and packaging, where multiple materials may be processed.
- Reduced Risk of Edge Damage: The moderate angle of a beveled edge provides sufficient edge stability to withstand moderate impact and wear, reducing the risk of edge damage, such as chipping or rolling. This enhances the longevity of the cutting edge and minimizes the need for frequent blade replacement.
Obtuse Angles on Beveled Edges
An obtuse angle on a beveled edge refers to an angle that is greater than 45 degrees relative to the surface of the blade. This angle creates a wider bevel, resulting in a stronger and more durable cutting edge compared to acute or moderate angles.
Benefits of Obtuse Angles:
- Increased Durability: Obtuse angles offer enhanced durability and edge stability, making them ideal for heavy-duty cutting tasks and abrasive materials. The wider angle provides more material behind the cutting edge, reducing the risk of edge damage and prolonging the lifespan of the blade.
- Improved Edge Retention: The wider bevel allows for better edge retention, meaning the cutting edge maintains its sharpness for longer periods between sharpening. This reduces downtime and maintenance costs associated with blade sharpening and replacement.
- Enhanced Strength: The wider bevel of obtuse angles provides increased strength and resistance to deformation, making them suitable for cutting through tough or challenging materials. This strength allows for more aggressive cutting action without compromising the integrity of the blade.
- Suitability for Abrasive Materials: Obtuse angles are well-suited for cutting abrasive materials, such as cardboard, fiberglass, and composite materials. The increased durability and edge stability of obtuse angles allow the blade to withstand the abrasive wear and maintain cutting performance over time.
- Reduced Friction and Heat Generation: The wider bevel can reduce friction and heat generation during cutting, resulting in smoother cutting action and reduced risk of material distortion or melting. This is particularly beneficial when cutting thermoplastic materials or materials prone to heat damage.
Application Considerations for Different Bevel Angles
The application considerations of bevel angles in the printing, packaging, converting, and processing industries encompass a variety of factors that impact cutting performance, efficiency, and product quality. Here are some key considerations for each industry:
- Printing Industry: The application considerations of bevel angles focus on achieving precision cutting and maintaining high-quality output. Printers require bevel angles that can deliver clean and accurate cuts on materials such as paper, cardboard, and film. Different materials may necessitate specific bevel configurations to ensure optimal cutting performance and minimize material waste. Additionally, edge retention is crucial in high-volume printing operations to minimize downtime for blade maintenance and replacement.
- Converting Industry: In this industry, the thickness of materials being processed is a significant consideration when selecting bevel angles. Thin materials may require sharper bevel angles for precise cuts, while thicker materials may benefit from wider bevel angles for increased strength and stability. Additionally, in high-speed converting processes, bevel designs that offer a balance between cutting speed and accuracy are essential to maintain production efficiency.
- Packaging Industry: In packaging applications, bevel angles must cater to the versatility demanded by cutting a wide range of materials, including cardboard, plastic films, and laminates. Clean cuts are essential to maintain the uniformity and aesthetics of packaging products, contributing to brand image and customer satisfaction. Given the abrasive nature of packaging materials, bevel designs with increased durability and edge stability are necessary to withstand the rigors of cutting through thick or tough packaging materials.
- Processing Industry: In the processing industry, the properties of the materials being used play a crucial role in determining the appropriate bevel angles. Materials with varying hardness, flexibility, and abrasiveness may require different bevel configurations to optimize cutting performance and prevent damage to the materials. Moreover, in processing operations involving temperature-sensitive materials, bevel designs that minimize heat generation and friction during cutting are essential to preserve product integrity.
In Conclusion
Selecting the optimal bevel design and angle for industrial cutting applications is crucial for achieving efficiency and maintaining product quality. By considering factors, such as material properties, cutting requirements, and operational conditions, industrial operators can make informed decisions to optimize cutting performance and productivity.
For expert guidance and customized solutions tailored to specific cutting needs, connect with the experienced team at Leverwood. With a wealth of knowledge and expertise in industrial knife manufacturing, our team can provide valuable insights and recommendations to ensure operations run smoothly and efficiently. Whether it’s precision cutting in the printing industry, clean cuts in packaging operations, specialized configurations for converting tasks, or optimized performance in processing operations, we are committed to delivering cutting-edge solutions that meet the unique needs of your customers.